

Você está aqui: Páginal Inicial >
Distribuição & Redes >
Consequências de um ar Ineficiente

A maioria das instalações industriais de compressores funciona com pressões desnecessariamente altas, entre 9 e 10 Bar. Porém a maioria dos sistemas necessitam na realidade de pressões bem mais baixas, geralmente entre 5,5 a 8,6 Bar. Cada 0,5 Bar reduzido na pressão do compressor pode significar uma economia de até 3% de energia.
Seguindo nosso propósito, abaixo informamos diversas consequencias de um sistema ineficiente a fim de conscientizar bem como orientar em relação ao uso de ar comprimido
Na maior parte das empresas, os compressores nunca são desligados durante à noite, por isso enormes quantidades de energia são consumidas para alimentar vazamentos de ar comprimido que consomem ar dia e noite. Além da eliminação dos vazamentos, uma simples parametrização de programação semanal com horários de partida e desligamento pode evitar um enorme desperdício de energia.
CONSEQUENCIAS DE UM SISTEMA INEFICIENTE
Soluções Inteligentes para Negocios
Visite nossas soluções para economia de ar comprimido.

Economia de energia
Já pensou em utilizar um compressor portátil nos horários de pico ?
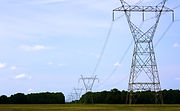
CONSEQUENCIAS DE UM SISTEMA INEFICIENTE
Um sistema de ar comprimido ineficiente poderá acarretar um aumento significativo nos custos de operação. Os prejuízos resultantes dessa situação decorrem de uma baixa pressão de trabalho, aumento do ciclo de operação dos equipamentos, baixa qualidade do ar e vazamentos.
Vazamentos
Os vazamentos merecem uma atenção especial, pois desperdiçam grande quantidade de energia. Na prática é impossível eliminar totalmente os vazamentos de um sistema, no entanto ele não deve exceder a 5% da capacidade instalada.
As tabelas a seguir apresentam o desperdício de energia provocado por vazamentos.
(tabela desperdicio de ar comprimido)
A metodologia apresentada abaixo, mostra como realizar uma medição quantitativa de vazamentos (controle tipo parada e partida e velocidade constante).
a-) Tomar um compressor com capacidade conhecida. Se existir mais de um, escolher, um com capacidade aproximada de 20% da capacidade total instalada.
b-) Todos os pontos de consumo de ar devem estar conectados normalmente, mas não em operação.
c-) A entrada em carga e alívio do compressor deve ser feita manualmente.
d-) São necessários dois cronômetros.
e-) Os níveis de pressão de carga e alívio são determinados pôr exemplo: carga : 6,5 bar e alívio : 7,0 bar
f-) Colocar o compressor em carga até a pressão atingir 7,0 bar. Pôr em alívio e acionar o cronômetro nº1 (mantê-lo em funcionamento durante todo o teste - T).
g-) Quando a pressão baixar para 6,5 bar, colocar o compressor em carga novamente e acionar o cronômetro nº2 (mantê-lo em funcionamento enquanto o compressor estiver carregando - t).
h-) repetir o teste cinco vezes.
i-) quando a pressão atingir novamente 7,0 bar no ciclo final, paralisar ambos os cronômetros.
Vazamentos=
Onde: Q - capacidade do compressor
t - tempo em carga do cronômetro nº2
T- tempo total do cronômetro nº1
Temperatura do ar
A temperatura de sucção do ar que será aspirado pelo compressor é um aspecto muito importante, pois quanto mais quente o ar, menor o rendimento da instalação.
Para cada 4ºC de acréscimo na temperatura do ar aspirado, o compressor consumirá 1% a mais de potência para entregar o ar nas mesmas condições.
Este aumento de temperatura diminui a massa específica do ar (massa de ar contida numa unidade de volume) em cerca de 1%, resultando também 1% a mais no volume. Para satisfazer essa condição é necessário captar o ar fora da casa dos compressores.
Exemplos:
A 15ºC a massa específica do ar é 1,225 Kg/m3
A 30º C a massa específica do ar é 1,164 Kg/m3 (- 5%)
Tubulação de admissão de ar
A tubulação de aspiração de ar deve ser projetada de maneira a ter o mínimo comprimento e o menor número de curvas possível a fim de minimizar a perda de carga.
Para cada 25 mbar de perda de carga na aspiração o rendimento do compressor irá cair 2%.
Capacidade de ar necessária
É de fundamental importância o conhecimento da quantidade exata de ar necessária para todos os equipamentos pneumáticos existentes. Uma estimativa abaixo dessa capacidade resultará em pressões inadequadas nos pontos de consumo e estimativas muito altas acarretarão grande investimento inicial e baixa eficiência do sistema.
A maioria dos equipamentos pneumáticos opera a 6 bar de pressão manométrica.
Para se conseguir esse nível de pressão no equipamento final é necessário um cuidadoso cálculo para se determinar a pressão de trabalho do compressor.
Devemos ter uma pressão de ar suficiente nos pontos de consumo. A pressão do ar exerce uma influência muito grande no desempenho das ferramentas pneumáticas. Uma pressão de trabalho muito baixa, diminui a potência dessas ferramentas, resultando aumento no tempo de operação e consequentemente aumentando os custos de produção. Uma das causas da baixa pressão nos locais de consumo pode ser a produção de uma quantidade insuficiente de ar
comprimido (é comum acrescentar novas ferramentas a uma linha já existente, sem verificar se isso afeta o desempenho do sistema).
Para evitarmos isso, devemos sempre ter um compressor de capacidade adequada a fim de manter a pressão nos pontos de consumo. Um sistema sobrecarregado, trabalhando além da capacidade original provocará uma baixa pressão nos locais de consumo.
Para obtenção da carga máxima do compressor será necessário somar o consumo total de todos os equipamentos consumidores existentes (em litros/s). A carga média do compressor é obtida multiplicando-se o consumo total de ar pelo fator de utilização (tempo estimado de trabalho de cada ferramenta durante uma hora).
Convém admitir uma tolerância de 10 a 15% da capacidade do compressor devido aos vazamentos e estimar o aumento da capacidade do sistema para futuras expansões também entre 10 a 15% ao ano.
Tipo de Controle do Compressor
O sistema mais indicado para racionalizar o consumo de energia é através da utilização dos inversores de frequência, pois desse modo o trabalho do compressor é ajustado em função da demanda de ar.
Manutenção do Compressor
Os custos operacionais são afetados diretamente pela eficiência de um sistema de manutenção. Uma manutenção adequada evita paradas de emergência aumentando a disponibilidade do equipamento para a operação.